Die Casting
The die casting process is to press molten metal into a mold under high pressure to form various complex shapes of door hardware parts. This process needs to be completed in a very short time to prevent the metal from cooling and solidifying. After the liquid metal is injected into the mold, it needs to be cooled and solidified. The cooling process is usually completed within a few seconds to a few minutes, depending on the size and shape of the part. After cooling, the part will be removed from the mold and processed later.
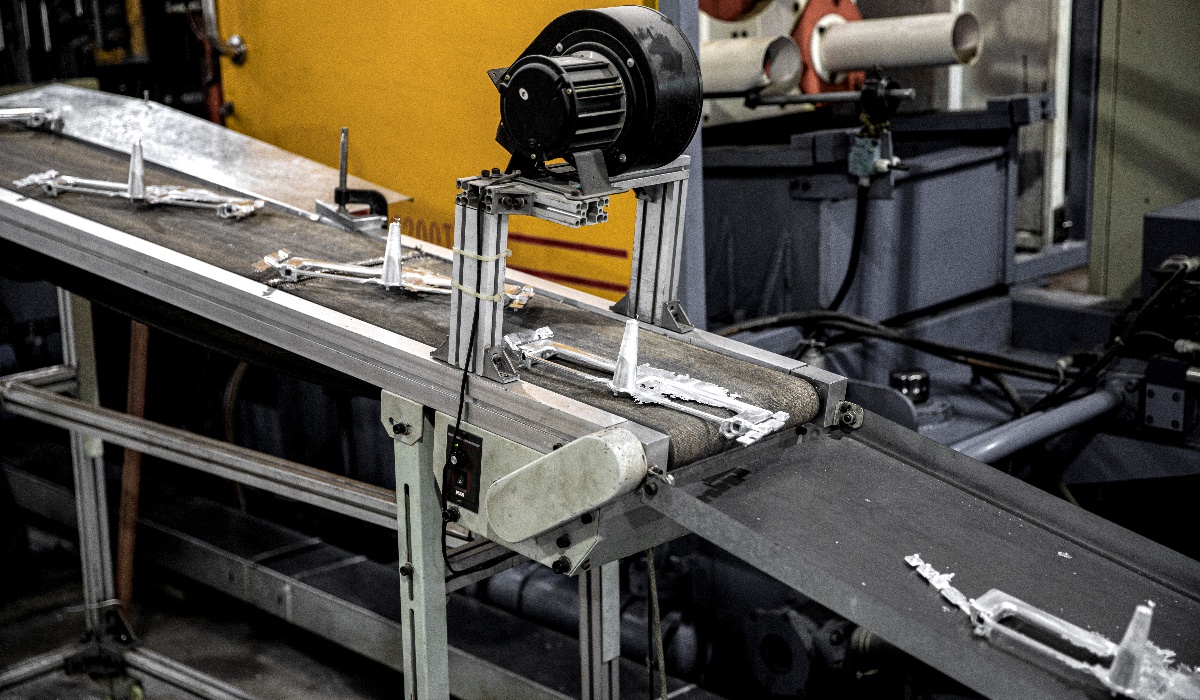
Machining
The blanks and die castings removed usually need some post-processing procedures, such as deburring, surface treatment, machining (drilling, tapping), etc. These procedures can improve the surface quality and dimensional accuracy of the parts to meet the design requirements.
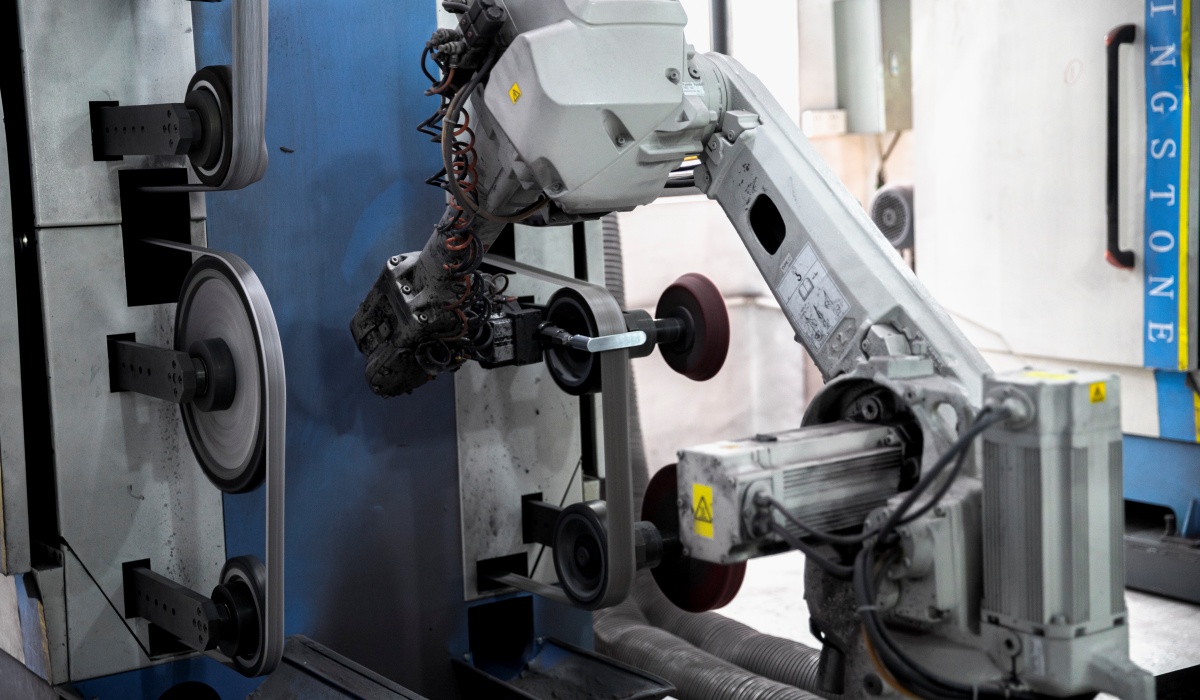
CNC (Computer Numerical Control)
The CNC process uses computer programs to control the movement and operation of machine tools, and can efficiently and accurately complete various cutting, milling, turning, drilling and other processing tasks for door hardware parts.
CNC machine tools can run continuously without human intervention, greatly improving production efficiency. The processing time of complex parts is significantly shortened, and the production cycle is significantly reduced.
By changing programs and tools, CNC machine tools can quickly adapt to the processing needs of different parts. This flexibility makes the CNC process suitable for small-batch, customer-customized production models.
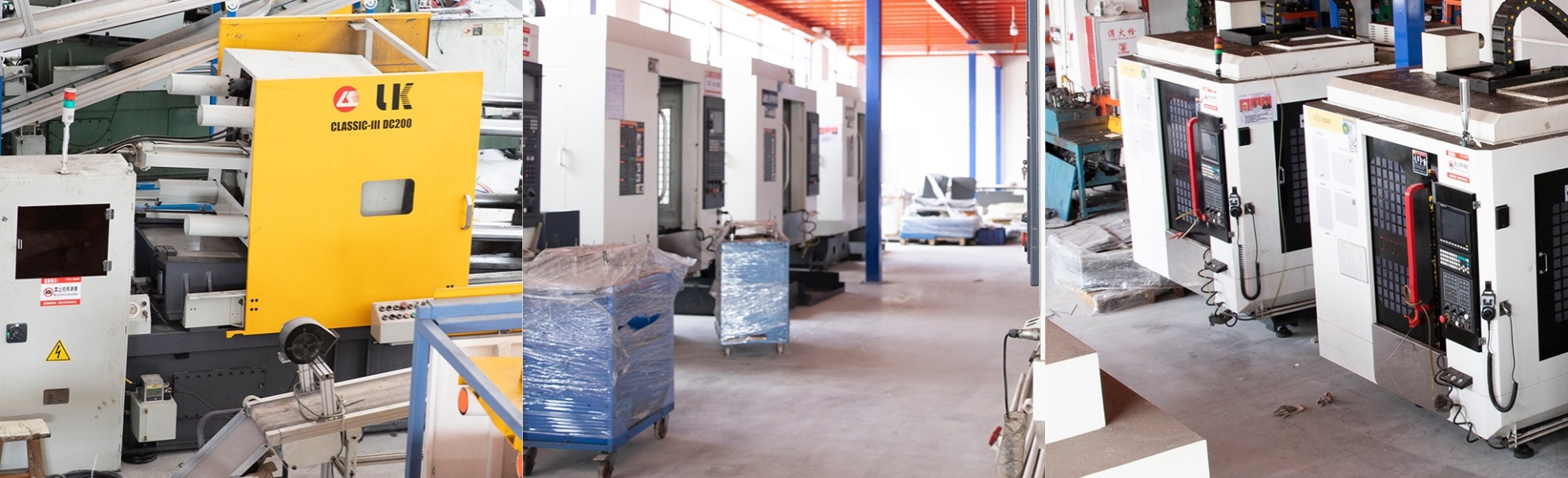
Polishing
Polishing is always important. We have our own polishing plant with around 15 experienced workers. First of all, we use rough (big abrasive grain) abrasive belts to polish the “flashes” and “gate marks”. Secondly, we use fine (small abrasive grain) abrasive belts to polish the shapes. Finally we use cotton wheel to polish the gloss surface. In this way, the electroplating will not have the air bubbles and waves.
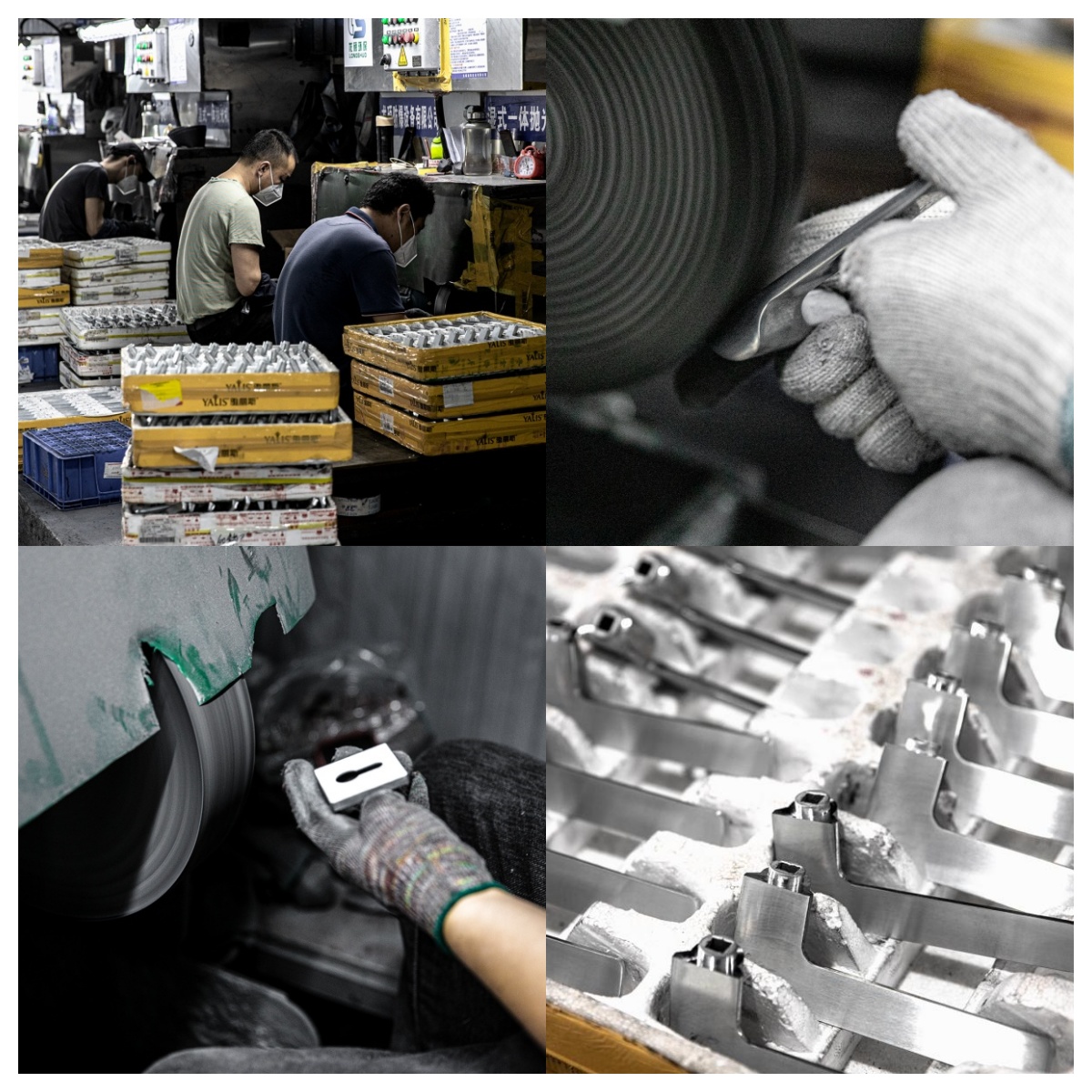
Surface treatment process: electroplating/spray paint/anodization
After the impurities on the surface of the hardware product are treated, it is time to add color. This process is called "electroplating" and the product that has undergone this process is called electroplated parts.
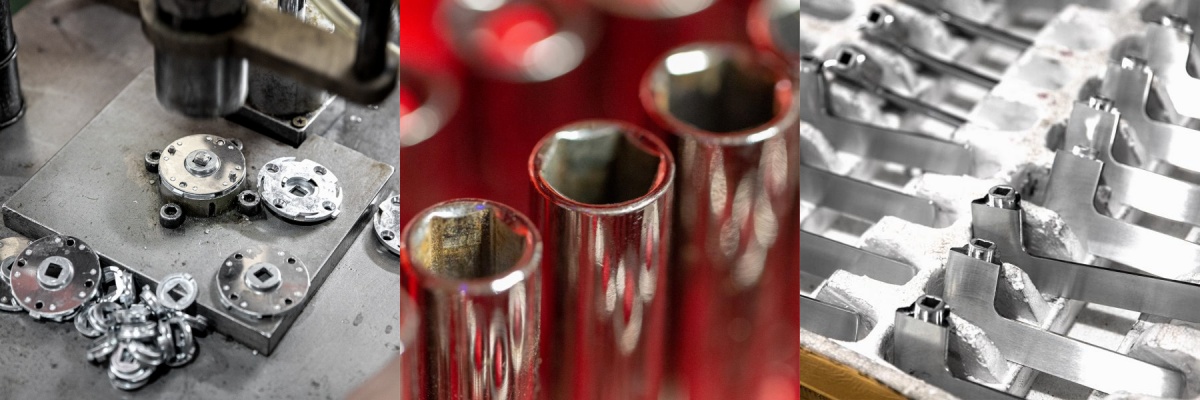
Assembly
Combination of handle and base: Combine the handle part and the base with screws or buckles, and ensure that the connection between each part is firm and not loose.
Functional test: After assembly, perform a functional test on the door handle to ensure that the rotation, switch and other operations are smooth and there is no jamming.
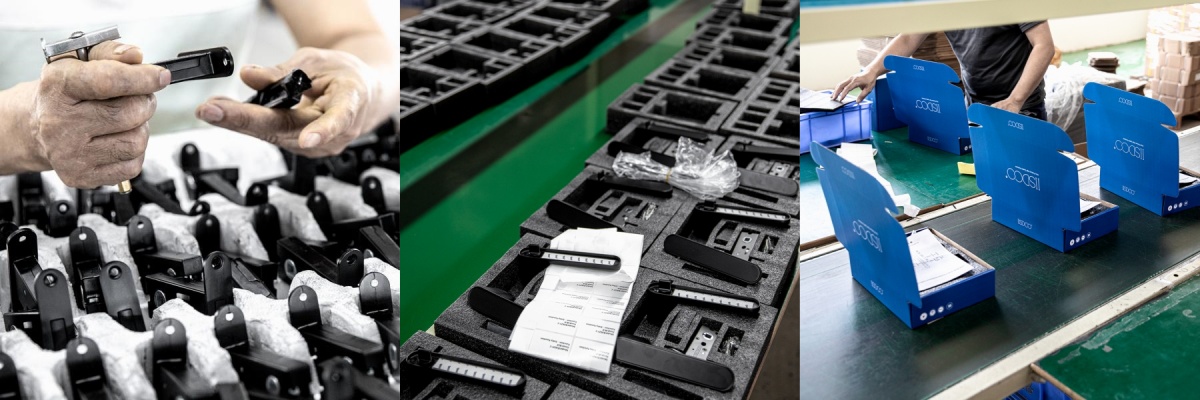